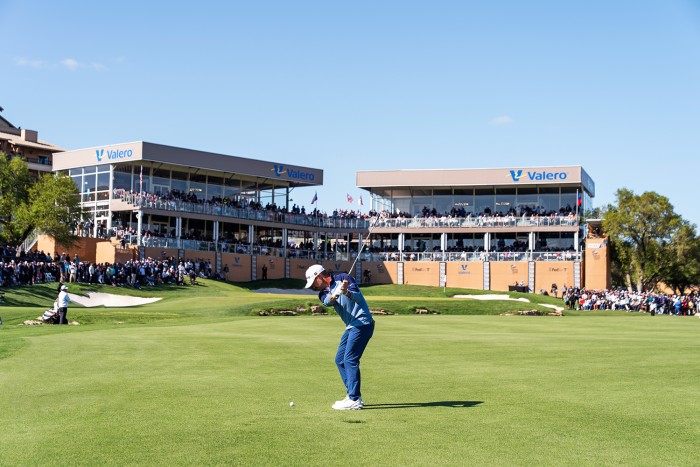
Committed to Giving Back and Making A Lasting Difference
A record $25 million raised through the Valero Texas Open and Benefit for Children to help improve lives of countless children and families.
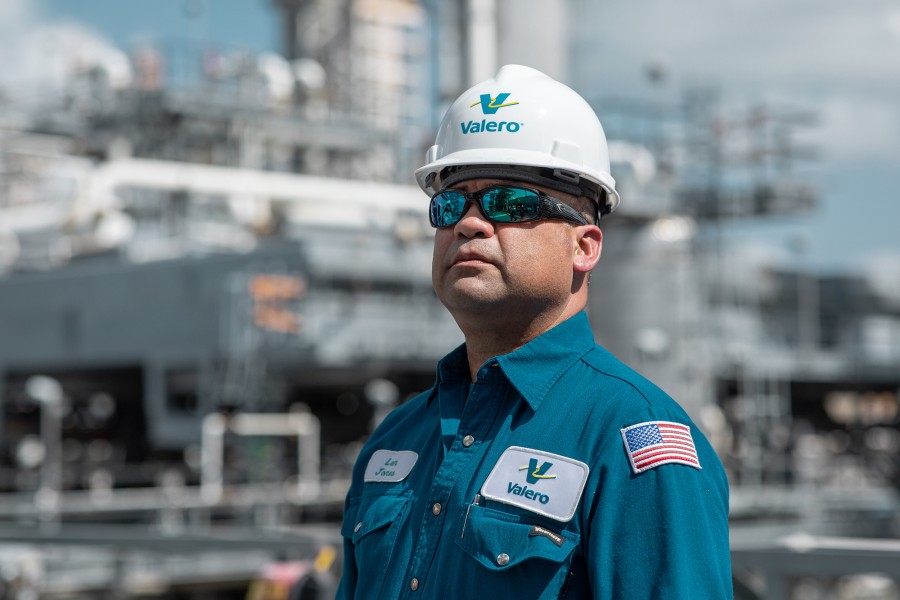
Safety is Our Foundation
For Success
We are focused on being the safest operator in our industry.
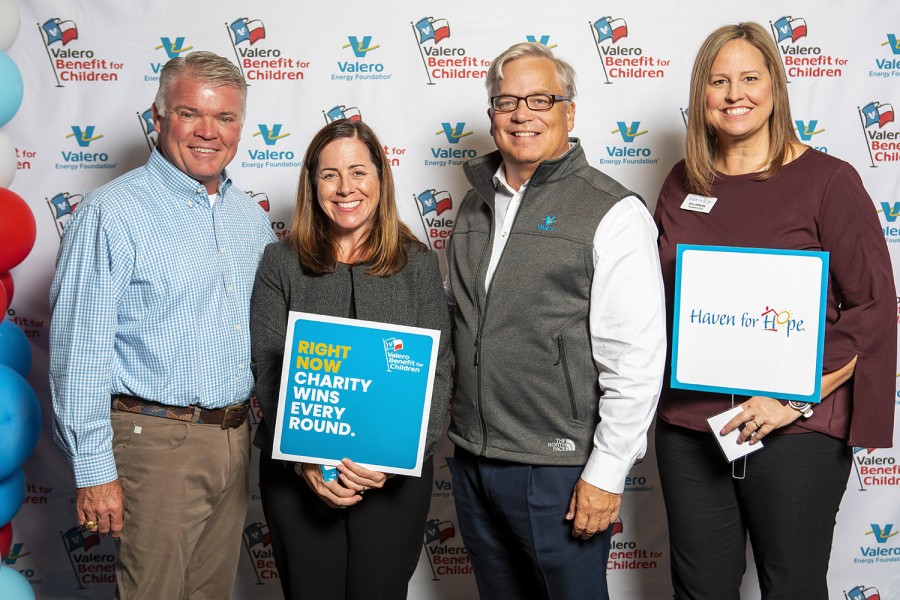
Philanthropy
Sharing our success with the communities where we live and work through volunteerism, charitable giving and the economic support of being a good employer.
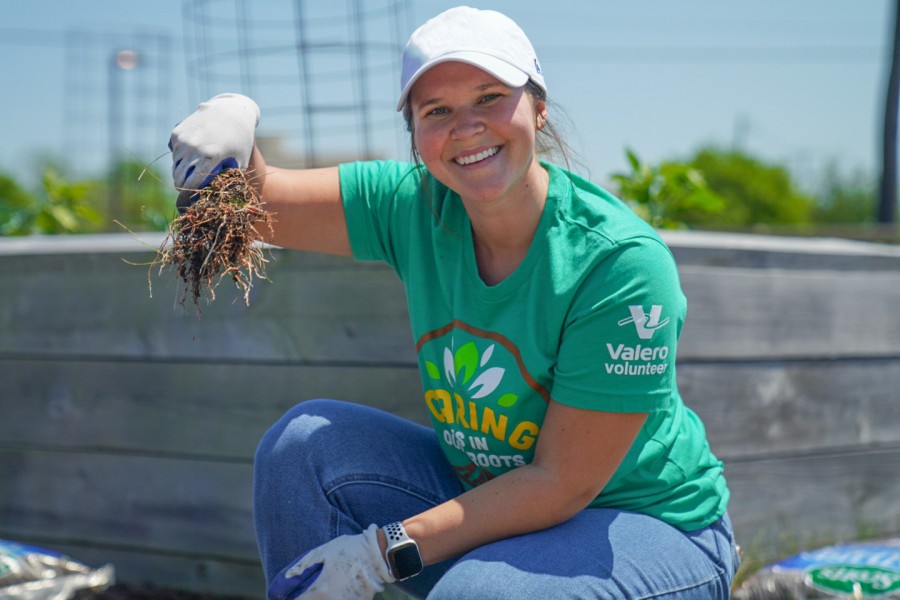
Volunteerism
Getting involved with the community and giving our time is at the heart of our culture. Over the past five years, our employees around the globe volunteered more than 600,000 hours of service.
Committed to Environmentally Responsible Operations
We have a demonstrated track record of environmentally responsible operations, large-scale production of low-carbon fuels for future generations and participation in environmental stewardship efforts in our communities.